Everything that follows would be only news of a disconcerting triviality if it had happened in our small European club where all is simple, with a portable telephone you call the manufacturer without time-lag and you have the piece following day without even to pass by custom.
For us it is all something else! When the problem appears at coffee time, it is already dark in Germany and our friends are comfortably installed in front of the TV with the family! For the cell phone it is necessary to be in town, it doesn’t operate even on the airports of San Martin or Esquel, but luckily, they work in Nahuel. For the customs, if you have the luck that the piece leaves in the 48 hours that follow the failure, it will be necessary to wait for a week before having it in hands after having paid 60% of custom and VAT!
At the first takeoff, the spring that maintains the lever of the flaps in locked position broke few meters above ground, making that the flaps pass in full negative and the glider sink. By luck my hand was on the throttle few centimetres from the flaps lever and I had the time to bring them back in positive before touching the planet…. But what makes the more pain, it is when it was necessary to reach this spring while cutting the fuselage to the disk cutter (Photo B2)! And as it was out of the question to wait for one week before flying, El Gringo, our genius of mechanics, constructed us the piece for the following day (Photo B1) while taking it from its rake (Photo B3) and of a thermostatic probe of an old fridge.
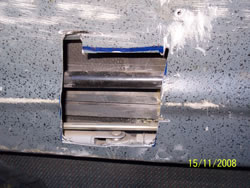
It was necessary to reach this spring while cutting the fuselage to the disk cutter
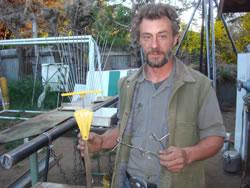
El Gringo
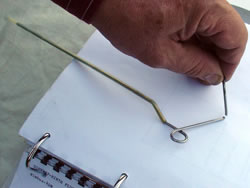
A thermostatic probe of an old fridge
Before the second flight we note that the wheel is burst! By luck we were at the parking lot and had a complete wheel with its hub. It is nevertheless a work of several hours. Some days later, it was the switch of the fuel pump that failed. There it is easier, it is standard.
But since we arrived to a strong odour of fuel worries me and as we already had seven failures of wing fuel tanks, I decide to disassemble the left tank, from where comes the odour, and therefore the glider! Surprised, it was not the reservoir that leaked, it was the hose that had become porous and let evaporate the most volatile components of the fuel. The phenomenon is especially serious when one uses green fuel 98 that contain extremely corrosive and smelling derivatives. This hose made of special rubber for fuel was only three years old and it had already died. It is necessary to banish the use of rubber therefore and to limit to the polyurethane, while sacrificing the thickness and therefore the safety in case of accident.
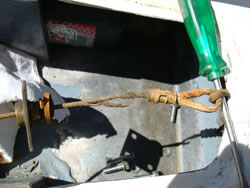
Two days later impossible to stop the propeller. By chance the incident takes place above the airport and will be solved in the day. The brake of propeller is in fact a roller bearing that goes into in a hole, this bearing is shielded and it is not possible to verify the state of the balls inside. Since this bearing never turns and that the same balls always undergo an effort in the same place, they ended up breaking and the external track of the bearing had moved some millimetres, just sufficient so that the brake doesn’t function anymore…
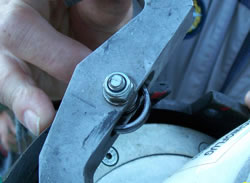
The following day we will burst once again, but during landing. The things complicate themselves because we occupy the runway and I had to repeat the operation of the past year, it was necessary to bring a crane and to work there, in the wind and the dust. Solution: one makes the compressor full, load it in the car, re-inflates the wheel and takes the glider out of the runway before it is deflated again, while repeating the operation as many times as necessary! By luck, we arrived at the parking at the first attempt!
At the time of the first flight upon my return in Europe, the device locking the gear failed. The beak in resin that blocks the lever crumbled, letting appear a metallic plate that rounded and started to cut the lever! And on top of all, the manufacturer installed a standard handle with the shape of pear that prevents the lever from revolving completely against the wall! The problem has been solved by “cutting the pear in two” (Photo B4) and replacing the fiberglass plate by another one made from Teflon with a changeable metallic plate, modification applied in standard since some time without warning the former customers.
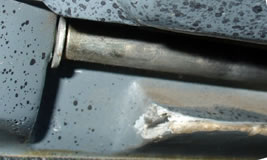
…letting appear a metallic plate that rounded
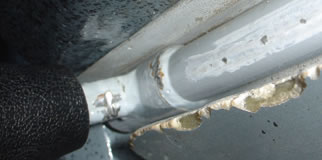
…started to cut the lever
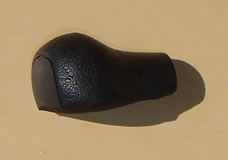
The problem has been solved by “cutting the pear in two”
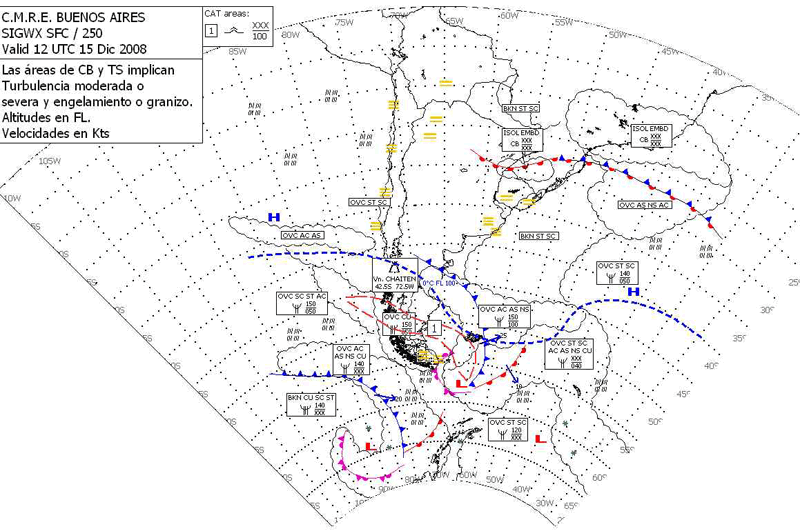